DESCRIPTION
The name of this product is derived from the venturi effect which states that, the fluid pressure is reduced when the fluid passes through the constricted section of pipe.
Venturi tube can be divided into 04 sections namely
- Inlet cylinder
- Inlet cone or convergent cone
- Throat
- Outlet cone or divergent cone
All these sections when connected together, forms venturi flow meter.
Venturi tubes gives accurate measurement of non-viscous fluids in clean as-well-as dirty fluids, manufactured strictly in accordance with ISO-5167, ASME MFC- 3M, BS-1042 etc. For critical measurement applications, wet calibration at reputed flow laboratories can be offered.
The unique geometry of venturi provides a smooth entry as well as smooth exit for the fluid. This causes a less pressure drop across the venturi i.e. the differential pressure is less. Low DP means low permanent pressure loss. Venturi can be used for a wide variety of applications that include air, water, vapor, steam, gas, chemical substances, sludge and slurry applications. Since divergent cone is provided at outlet of venturi, the pressure recovery is very good. Thus it reduces operating costs and also reduces straight length requirement.
Typically the convergent angle is fixed to 21°. Divergent angle can be varied between 7°- 15° without any effect on the pressure loss and discharge coefficient.
Venturi tube is also referred as Classical venturi or Harshell venturi.
CLASSIFICATION
Venturi tube is broadly classified as truncated or Non truncated venturi.
The venturi is called as Truncated when the outlet cone diameter of the venturi is less than the pipe dimension. When the same is equal to the pipe diameter venturi is called as non truncated type venturi.
The divergent cone can be truncated about 35% of its length without affecting the discharge coefficient.
Further the venturi is classified in 3 basic types, as given below:
- MACHINED TYPE
- FABRICATED TYPE
- AS CAST TYPE
SALIENT FEATURES
- Specifically useful for low pressure and low pressure drop area.
- Can be used for fluids containing dust of suspended particles.
- Short upstream and downstream length required.
- Low permanent pressure loss & high pressure recovery
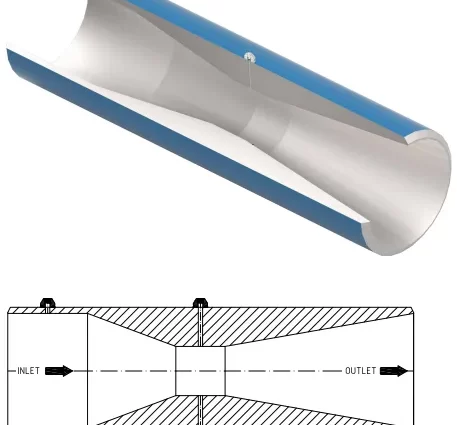
MACHINED TYPE VENTURI
Machined venturi is manufactured by machining the required profile from a solid forged bar. The sizing and dimensional guidelines are mentioned in ISO-5167 part IV.
Depending upon the customer requirement, the end connection can be either BWE or Flanged.
- Size limits >> 50 mm to 250 mm.
- Uncertainty in discharge coefficient >> ± 1%
- ReD >> 2 x 10^5 to 1 x 10^6
- β >> 0.4 to 0.75
Materials: The venturi can be supplied in any material including plastics. The materials generally used are SA105, SA182F316/L, SA182F304/L, Inconel, Duplex SS, Monel etc.
Venturi upstream pressure tap is located at the mid of inlet cylinder & the downstream pressure tap is located at midpoint of the throat.
When averaging is required, the pressure tapping can be taken through piezometric ring or also called as annular ring. This can be manufactured from forging or can even be fabricated from rolling the pipes, as per requirement.