DESCRIPTION
In a typical process plant, there is a high demand of saturated steam for various heating applications & process requirements since saturated steam has good heat transfer efficiency. However the boiler generates superheated steam.
We have proven track record of successful operations of desuperheaters (DSH) in Venturi type and Variable Area nozzle type.
Amount by which superheated steam temperature exceeds the saturation temperature at particular pressure, is called as degree of superheat.
PRDS System is used to reduce the steam pressure to required operating pressure & to reduce steam temperature closure to saturation temperature.
Suitably designed pressure control valve, reduces the steam pressure to desired operating pressure. During this process, the temperature also reduces following the superheated steam curve. But the degree of superheat remains unaltered.
The superheated steam temperature is reduced close to saturation temperature, by injecting water into high pressure, high velocity steam by controlled water flow through water control valve & desuperheater.
Conventionally the pressure reduction & temperature reduction is done in two different units.
- Skid in which only pressure reduction is done, is called as PRESSURE REDUCTION STATION (PR Skid)
- Skid in which only temperature reduction is done, is called as DESUPERHEATING STATION (DSH skid)
- Both Skids combined, is called as PRESSURE REDUCTION & DESUPERHEATING STATION (PRDS Skid)
MATERIAL FOR PRS / PRDS / DSH STATION
- Steam inlet isolation valve
- Steam pressure control valve
- Steam outlet isolation valve
- Steam bypass valve (manual/control)
- Pressure gauge @inlet & outlet
- Temperature gauge
- Rtd temperature sensor
- Safety relief valve
- Desuperheater
- Steam piping
TESTING / CERTIFICATIONS REQUIRED
- Hydro testing
- Dp testing
- Radiography
- Ibr certification
- Asme certification (in case of exports)
- Performance test of dsh
- Calibration / performance test for control valves.
MATERIALS SUPPLIERS
- Isolation valves: ksb, bdk, seel strong, l&t, audco, bv valves
- Control valves: mil controls, fisher, dresser valves, il-palakkad.
- Safety relief valves: fainger laser, tyco sanmar.
- Strainer: gujarat ottofilt, precision, pennent, precision.
- Desuperheater: fepl, chemtrols, forbes marshall.
- Temp. Gauge/elements: pyro electricals, gic, wika.
- Pressure gauge: pyro electricals, gic, wika.
- Pressure / temp. Transmitter: yokogawa, honeywell
TYPICAL PRS STATION
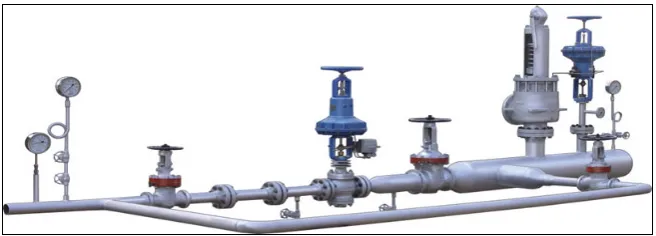
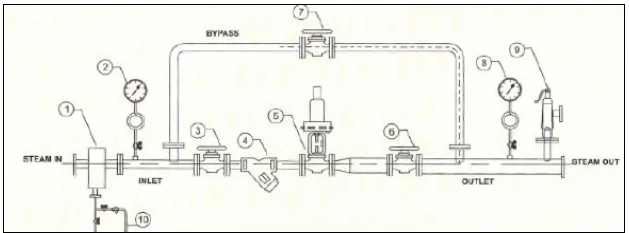
TYPICAL DSH STATION
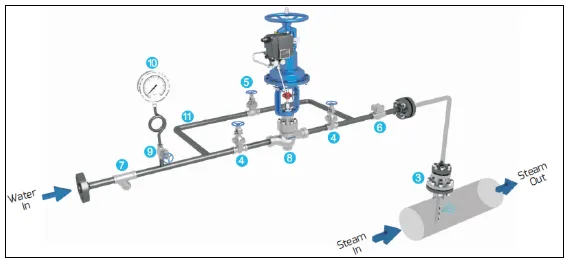
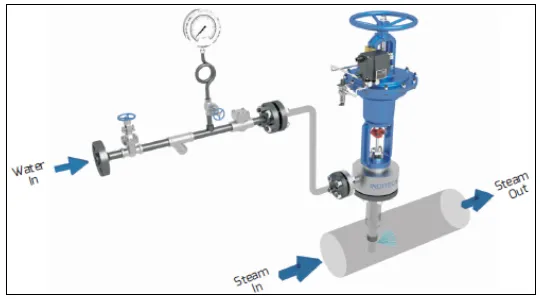
TYPICAL PRDS STATION
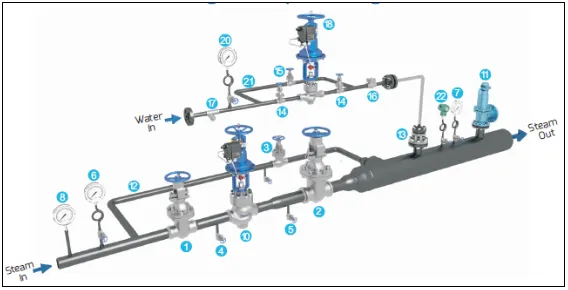
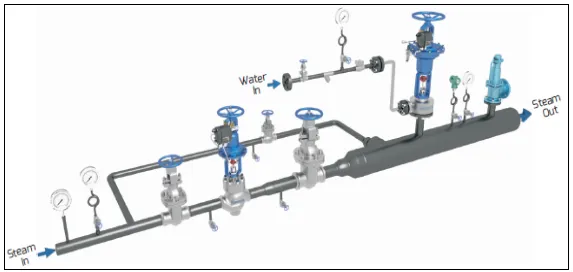
DESUPERHEATER (DSH)
Desuperheater (DSH): means to reduce the excess superheat. Means by which this is achieved is called as desuperheater.
Type of desuperheaters (DSH) as per combination with valve, as below:
- Desuperheater (DSH) with saperate spray water valve.
- Desuperheater (DSH) with integral control valve.
- Type of desuperheater (DSH) as per construction:
– Venturi type dsh.
– Variable section spray nozzle.
VENTURI TYPE DESUPERHEATER (DSH)
The Desuperheater (DSH) model is a non-integral type, which requires a separate spray water control valve.
This is a venturi design with sharp edge against the flow- guarantees a high steam velocity and well atomized cooling water in the point of injection.
The cooling water enters the nozzle via the water flange. The pressure difference between the cooling water and the steam, to ensure good controllability and satisfactory atomization of the injected cooling water should not be below 2 bar.
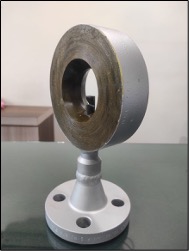
This desuperheater (DSH) model is made for installation in steam pipes 1” to 4” . This type of DSH is, as standard, mounted between flanges
This desuperheater (DSH) model is made for installation in steam pipes 1” to 4” . This type of DSH is, as standard, mounted between flanges
VARIABLE AREA TYPE DESUPERHEATER (DSH) : Single nozzle
In order to maintain a constant pressure inside the injection nozzle, the later is preloaded by a spring calibrated in function of the water/steam differential pressure.
Any load variation in the external water control valve is immediately compensated by change of orifice of the nozzle. Depending upon customer piping requirement, this DSH has 02 configurations.
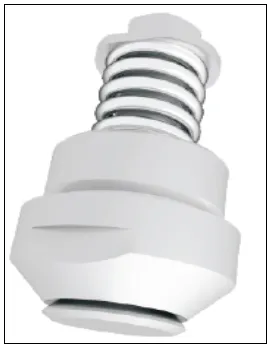
Angle connection Straight connection.
There are 03 nozzle sizes available, based on the water quantity & differential pressure between water & the steam. This DSH can be used from 6” upto 40” line size. (steam pipe size).
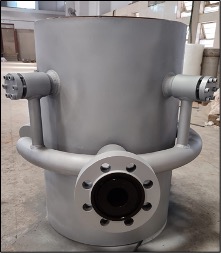
VARIABLE AREA TYPE DESUPERHEATER (DSH): Multiple nozzles
The Desuperheater (DSH) model is a non-integral type, which requires a separate spray water control valve.
CD-M desuperheater (DSH) is used in desuperheater (DSH) applications where large spray water flows are required for cooling of the steam.
It is a part of steam line with a number water atomizing nozzle, nozzles attached to it.
The nozzles are connected to a common spray water pipe connection. The water flow is controlled by separate spray water control valve. The nozzle is variables orifice.
The nozzle body is screwed in to the nozzle holder, which housed the nozzle and distributes to water to the nozzle
TYPICAL INSTALLATION DRAWINGS OF DSH
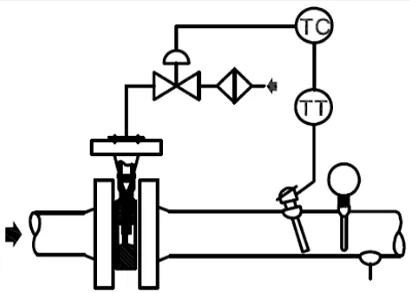
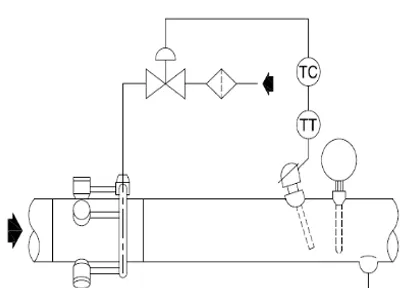
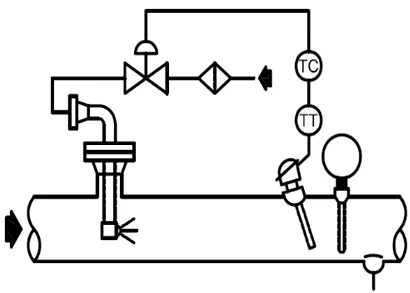
We are specialised in desuperheater (DSH) manufacturers in India