DESCRIPTION
An orifice plate is a thin plate with a hole in the middle. It is usually placed in a pipe in which fluid flows. When the fluid reaches the orifice plate, with the hole in the middle, the fluid is forced to converge to go through the small hole; the point of maximum convergence actually occurs shortly downstream of the physical orifice, at theso-called vena contracta point.
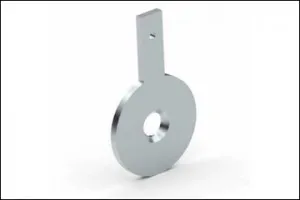
As it does so, the velocity and the pressure changes. Beyond the vena contracta, the fluid expands and the velocity and pressure change once again. By measuring the difference in fluid pressure between the normal pipe section and at some specific point after orifice plate, the volumetric and mass flow rates can be obtained from Bernoulli’s equation. We are specialised Orifice Plate Manufacturer.
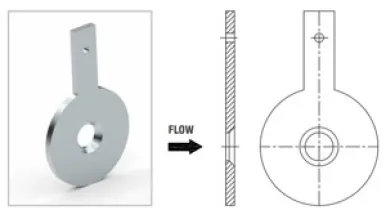
CONCENTRIC ORIFICE PLATES
These are most commonly used for flow measurement. This has special features such as simple structures, high accuracy, and ease of installation and replacement. These plates are recommended for clean liquids, gases & steam flow, when the Reynold number ranges from 10000 to 10^7.
QUADRANT EGDE ORIFICE PLATE
The inlet edge of the bore of this orifice plate is rounded to a quarter circle. This orifice plate is usually used for viscous fluids & Reynolds number between 1500 & 10000.
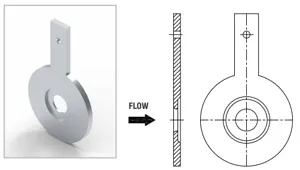
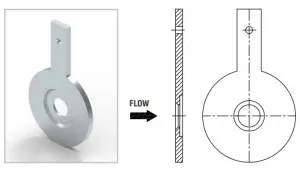
CONICAL ENTERANCE ORIFICE PLATE
The inlet edge of bore of this plate is conical in shape. This plate is used for highly viscous fluids with Reynold’s number 80 to 1500.
ECCENTRIC ORIFICE PLATE
For liquids containing solid particles that are likely to sediment or for vapors likely to deposit water condensate, this orifice plate is used with its eccentric bore bottom flush with the bottom of the piping inside surface so that the sedimentation of such inclusions are avoided. Likewise, for gases or vapors, it may be installed with its eccentric bore top flush with the ID of the piping to avoid stay of gas or vapor in its vicinity.
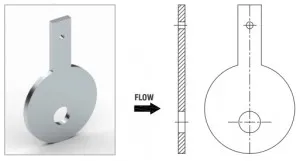
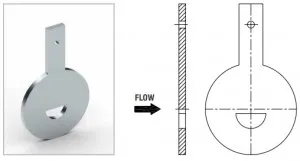
SEGMENTAL ORIFICE PLATE
Segmental orifice plates are most useful where there are substantial entrained water or air and also if there are suspension in the fluids. This avoids build up in front of the orifice plate. The orifice hole is placed at the bottom for gas service and top for liquids
ORIFICE WITH RTJ HOLDER
RTJ holder with plate is used when the orifice plate is used at high pressure & high temperature. When normal gaskets cannot be used due to more pressure-temperature, RTJ gaskets are used for leak prevention.
These are available in oval or octal shapes. The Orifice Plate is Universal type and fitted on the RTJ holder with the help of screws. The RTJ holder material is selected such that it will be softer than the flange. The plate material will be as per process requirement.
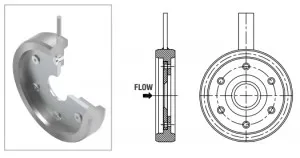
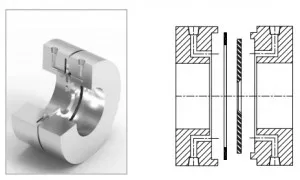
ORIFICE PLATE WITH CARRIER RING
Carrier ring type construction is used facilitate pressure taps, when it is not possible to drill taps on flanges. This construction is used below 2″ line size, but not restricted. Carrier ring can be Male-Female type OR one piece construction. Single piece construction is chosen when direct mounting of DPT is required. Also for bigger sizes, single piece carrier is more cost effective.
RESTRICTION ORIFICE PLATE
SINGLE STAGE
The restriction orifice plates are used for reducing fluid pressure. When the required pressure is dropped with only one plate, it is called as single stage restriction This plate is similar to the Square edged Concentric plate, except that the bevel is not provided for restriction orifice. Since the purpose to drop the pressure & not to reduce pressure loss. The plate thickness is calculated based on the required pressure drop across the plate.
TECHNICAL SPECIFICATION
- Size of PIPE & Schedule.
- Size of Flange/Type/Rating/Schedule/Standard.
- Gasket: CAF / SS Spiral Wound + CAF / PTFE / PVC / Rubber, Other materials as per special request.
- Stud / Nut: ASTM A193 Gr. B7/ASTM A194 Gr.2H, B7M/2HM, A193 B16/A194 Gr. 4
- Design Standards: ISO 5167/ BS 1042 / RW Miller / ISO TR-15377.
- Flanges: ANSI B-16.36/B16.5/AWWA/ASME B16.47/ IS 6392 / BS 10 etc.
- Orifice Plate Types: Square edge concentric, Quadrant edges, Conical entrance, Eccentric, segmental, Restriction.
- Pressure Tappings: Flange Taps / Corner Taps / Radius taps
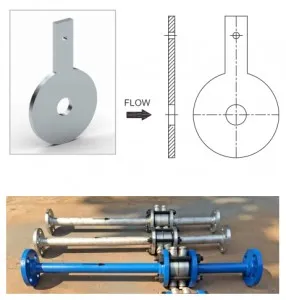
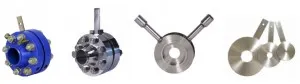
Materials
- Flanges: Carbon Steel, Low Temperature Carbon Steel, Chrome Moly Steels, Stainless Steel, Duplex, Super Duplex, 6 Mo, Monel, Hastelloy, Incolloy 825, PVC, PP, PVDF.
- Orifice Plate: Stainless Steel, Duplex, Super Duplex, Monel, Hastelloy, Inconel etc.
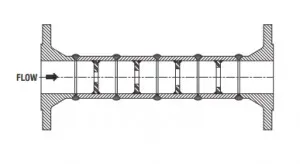
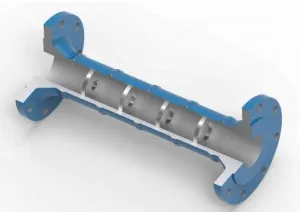
MULTISTAGE RESTRICTION ORIFICE PLATE ASSEMBLY
This is the next version of single stage restriction orifice plate. When the pressure is dropped across the orifice plate, the velocity is increased by large.
For gas service, when the drop is nearer to 50% or more, this velocity approches the velocity of sound or becomes more than that of sound velocity. The point at which the velocity is equal to the sound velocity, is called as Sonic condition.
The sonic condition is not favourable for process line, since it creates noise & vibrations. Also more valocity causes errosion of plate bore.
To avoid all these, the pressure is dropped in number of plates arranged in series. The assembly of all these plates combined, is called as multistage restriction orifice plate assembly.
For liquid service, sonic condition is replaced by cavitation/flashing phenomenon. When the pressure line line falls below the vapour pressure of the fluid, cavitation starts. The cavitation is harmful for the piping and instruments fitted after the orifice plate.
For liquids, the deciding factor for the requirement of multistage is cavitation index. To avoid cavitation, the index is maintained below 2. i.e. the pressure is dropped in such a way that the cavitation index for each plate is below 2.
For constriction of MSA, the orifice plate suitable for mounting inside the pipe, are arranged in series. The distance between two plates is maintained equal to 1D i.e. 1 pipe ID. The complete assembly with no. of required stages welded inside the pipe, is called as Multistage Restriction Orifice plate assembly.
The end connection can be either BWE or Flanged, depending upon the requirement.
The selection of multistage depends upon the application or location where the pressure reduction is desired. If the application is venting in atmosphere, exhaust to flare tank etc. then the increased noise level is also accptable. In that case mulsistage is not selected.
The multistage can be supplied with IBR certifications, whenever required. Also NDT testing like Radiography, DPT can be done as required.
ORIFICE PLATE WITH METER RUN
When the orifice plate assembly is supplied with piping spool on upstream & downstream, the complete assembly is called as Meter run Assembly. The orifice assembly can be any one type as defined in earlier pages.
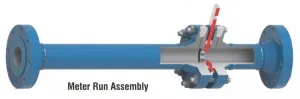
Meter Runs are supplied as a complete unit to ensure the necessary straight pipe lengths are available for the maximum accuracy. They can be supplied with temperature tapping if required. For gas application where maximum accuracy is desired the meter run is supplied with flow straightner with honed pipe at inlet side as per AGA standard.
Carrier ring type meter run is used where the tapping on flange is to be avoided or not possible. e.g. with PVC/PP flanges.
- Standard Lengths 1000 mm. Other lengths on request.
- Standard Tappings 1⁄2″ NPT female (two nos. per flange) others on request.
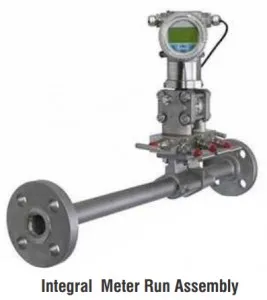
INTEGRAL METER RUN ASSMBLY
This type of assembly is specially constructed for direct mounting of DP transmitter. The maximum size available for this type is 1.5″. For the construction of this, specially designed integral blocks are used, the shape of which is made suitable for DPT mounting. The plate is made to suit the integral blocks. Integral MRA uses a corner tapping arrangement, hence the accuracy is better than the conventional type meter run. Additionally, this arrangement reduces the losses through leakage, since there are no leakage points. But, as the DPT is mounted directly on the meter run, this can be used upto 120deg maximum only.
- Sizes available: 1/2″ to 1.5″
- Materials available: CS, SS304, SS316
- Pressure rating: up to 600#